A dearth of relevant up-to-date knowledge about one of construction’s principal structural materials threatened to hinder the biggest ever programmed to rebuild and revitalize England’s many concrete roads. A dearth of relevant up-to-date knowledge about one of construction’s principal structural materials threatened to hinder the biggest ever programmed to rebuild and revitalize England’s many concrete roads. The Concrete Roads Programmed is now well underway with renewal of the A11 at Norwich. “Relatively little had been done around concrete development for 20 years and catch-up was urgently required,” declares National Highways Concrete Roads Centre of Excellence technical lead Michael Ambrose. This became clear in 2019, ahead of Road Investment Strategy 2 (RIS2) – covering the period 2020 to 2025 – and the commencement of National Highways’ Concrete Roads Programmed to reconstruct or extend the life of England’s 644km of concrete roads. Construction activity began in 2020, with Ambrose expecting the programmed to be complete within RIS6 to RIS8, meaning a possible finish in 2060. Concrete technology needed to be transformed in respect of recycling and reuse, reduced CO2 footprint and more generally, via thinking out of the box,” Ambrose says. There was also concern within National Highways that concrete was not being “promoted” sufficiently to young engineers and that old hands with practical roads-related experience of the material were retiring from the industry – meaning a potential skills shortage to come. “So it was decided right away – in 2019 – to establish a concrete roads Centre of Excellence (Coffer),” Ambrose says, “which I head up.” The center was assigned terms of reference that include combining advances in concrete technology, safety and environmental practice to make better, longer lasting roads; plus securing the interest of a new generation of engineers.
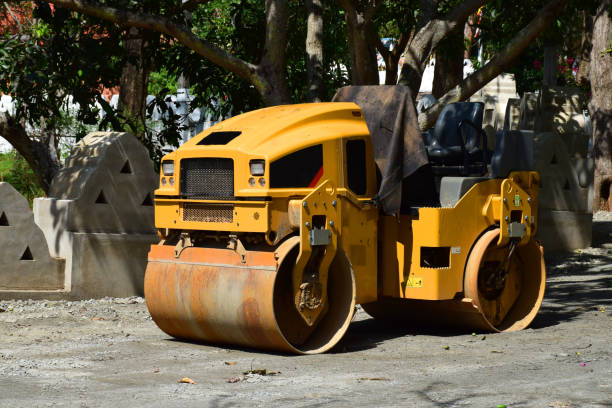
From The Start, Coffer Was Conceived As a Virtual Entity.
meaning it has no research and development (R&D) infrastructure of its own. The Centre effectively serves as an agency which commissions what R&D needs to be done to suit its priorities. “I have just three colleagues in my team. We cooperate – inter alia – with the intelligent materials section of Cambridge University, helping steer the university’s digital roads programmed,” Ambrose says. “We also work with Derby and Northumberland universities; consultants such as Secom, Mott MacDonald and Sseko and contractors like Costain.” Recycling and reuse of concrete had to be an early priority as it was a big issue – not least in keeping the Concrete Roads Programmer’s carbon footprint to a minimum and contributing to the circular economy. “RIS2 was going to involve coping with 400,000m2 of recovered concrete – good Type 1 – most of it to be earmarked for use in reconstruction projects or handed over for other schemes. “Upscaling had to be considered: normally 20% of old concrete is recycled, we now wanted to encapsulate 80% to create slabs and barriers and other components. “We also wanted to look at the actual cost of recycling core products, including in terms of generating CO2, as well as the cost of upcycling. Before, it was too expensive to upcycle, but now the rising cost of new materials means innovative processes could be viable, with beneficial effects.” Changes in carriageway construction Take, for example, recycled concrete going into sub-base. With oil [prices] going up and the cost of recycled aggregates effectively going down, this could lead to changes in carriageway construction. Roller compacted concrete and concrete/asphalt composites might be more feasible, leading to reductions in programmed and lorry miles and thereby CO2, Ambrose says. “If you don’t do the research, you can’t see the savings,” he adds. Coffer is also involved with research into how recycled concrete can be washed and cleaned to bring its constituent components back to the condition of virgin materials so fines can be reused in asphalt or other products. Another early priority for the center has been non-destructive surveying of concrete pavement to detect defects without having to damage and/or close roads.
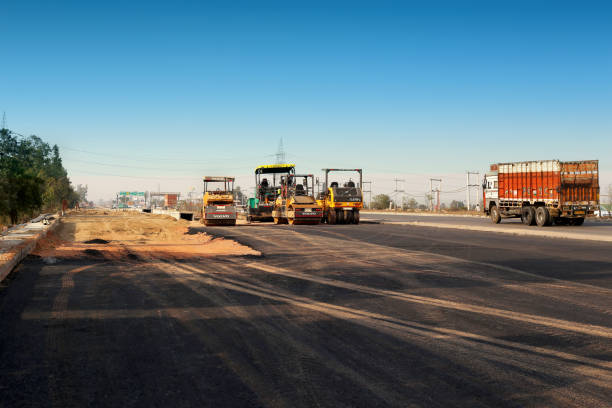
“The Usual Method of Coring Is Highly Destructive.
weakening a carriageway’s structural homogeneity and often leading to prolonged closures,” explains Ambrose. “We’ve been looking in particular at 3D GPR (ground penetrating radar) using Lidar (laser imaging detection and ranging) to capture photos of 4K resolution.” Non-destructive surveying Vehicle mounted, the system provides high resolution visual data about the state of the concrete road being travelled over. But Coffee demands more from its GPR surveys than just that. “The survey results are drawn on via machine learning and automation to tell us what needs to be repaired,” Ambrose says. “The information moves to a portal which collects and stores data to create a digital record of all the work undertaken, from when the defects are seen, to their rectification, to the monitoring of their future performance. “It’s a ‘golden thread’,” he adds, “a cache of information that is easily accessible and which allows the supply chain to visit and see the roadworks design in real time, as it is updated.” Information is shared with everyone, quickly. Beyond that, over time the end result is an accurate and priceless source of what has been done to a carriageway and where. Ambrose goes on to provide a snapshot of other Coffer activities, including the search for better solutions for concrete repair; intelligent joint sealants, which change color to warn of slab movement; and longitudinal diamond grinding to improve the noise characteristics of aged but sound concrete pavement. “Reducing noise from concrete roads is important, probably the biggest benefit we can bring, from a public point of view, particularly to people living near a noisy road,” Ambrose says. “But there are other benefits like less driver fatigue and lower resistance to tyros, meaning lower CO2.” Returning to National Highways’ Concrete Roads Programmed, Coffer is providing guidance on concrete removal and reuse and is on standby for problem solving.
Regarding its obligation to promote the industry to young people, CofEx is concentrating on education including school visits and post-graduate programmes, such as one in concrete pavements and construction management at the University of Derby. “The level of interest is astonishing,” he says.
Recent Comments