Steel has long been the backbone of construction, but with prices rising and embodied carbon targets pressing, basalt rebar could become an alternative. Basalt reinforcement as an alternative concrete reinforcement to steel or fiberglass is not a new technology. Some countries around the world, most notably the United States, have been using it for decades. In the UK it is still an emerging option, but is growing in prominence as decarbonization efforts intensify. Applications on High Speed 2 (HS2) and a major project on the M42 are helping to raise the profile of basalt rebar and highlight its potential. The reinforcement is made of what is called basalt fiber reinforced polymer (BFRP). To create the fibers, volcanic basalt rock is collected, crushed into small pieces and melted at 1,400°C. The silicates in its formation enable the melted basalt to become a liquid that can be gravity stretched through a special plate to form long filament strands. These filaments can be thousands of meters long and can be spooled until they are ready to be formed into reinforcement. The rebar conversion is done through pultrusion, where the fibers are pulled under tension and then immersed in liquid epoxy resin. The resin is a polymer bond that is heated to liquid form, into which the threads are immersed. It then cures within minutes to become the finished bar.
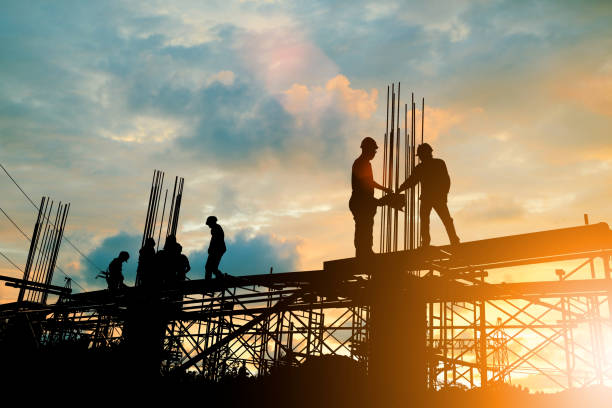
\
Basalt Rebar Was Used In the Guide Walls for Diaphragm Wall Construction on HS2
The benefits of BFRP over steel are numerous, according to Malcolm Newton, a director of ba The benefits of BFRP over steel are numerous, according to Malcolm Newton, a director of basalt rebar manufacturer Bartech. It is easier to work with during construction because, compared to steel, it is 4.5 times lighter and has 2.5 times the tensile strength. As an inert material, basalt is resistant to alkalis and acids, making it ideal for structures exposed to wet conditions as it does not corrode.\ Its corrosion resistance contributes to a reduced carbon footprint for the reinforced concrete. With water ingress not an issue, basalt rebar requires 20% less concrete cover in a slab compared to steel bar, according to Newton. Basalt rebar’s carbon footprint is significantly lower than steel too. This may seem counter-intuitive given the rock has to be imported from the United States and is heated to a high temperature. But Newton says that lifecycle analysis from Kingston University has shown that it uses at least 70% less carbon during the production process than steel reinforcement and 22% less than recycled steel. There are areas where basalt does not match up to steel. It cannot be bent like steel and, despite its higher tensile strength, it has lower elasticity. These are factors that mean that contractors are unlikely to use it in tall vertical structures. Slow adoption in the UK
Newton believes price has been the main reason for BFRP’s slow adoption in the UK, but he expects this to come down if more is produced. While steel prices are rising, that of basalt has remained stable to a point where it is now almost comparable to that of steel. “So for a long time no one ever thought about using alternatives to steel because it was cheap, easy to use and easy to sign off on professional indemnity,” Newton says. There’s also no Eurocode for fiber reinforced polymers of any kind, including basalt rebar, because there is limited testing knowledge and the industry is “conservative by definition”, according to Newton. As a result engineers are reluctant to specify it. “However, Bartech’s structural engineers are able to provide design assisted by testing,” Newton says. “With a combination of tests and calculations carried out in our laboratories, our engineers can provide designs acceptable with the Eurocodes and more importantly provide designers with professional indemnity.”
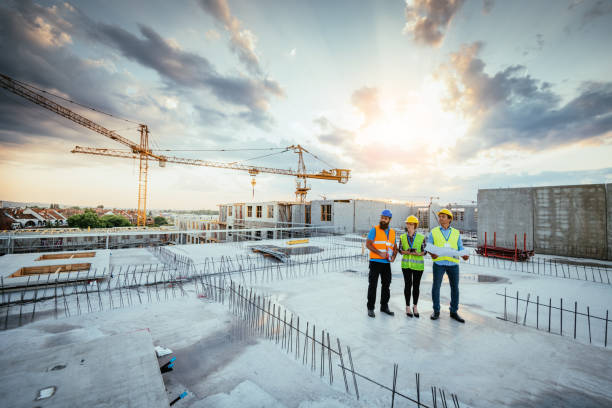
Thompson’s Bridge
One UK project has displayed the benefits of using basalt – backed up with long term analysis. The deck for Thompson’s Bridge, a road bridge in Northern Ireland which opened in 2011, was constructed using BFRP instead of steel reinforcement. The project, led by a team from Queen’s University Belfast’s School of Planning, Architecture & Civil Engineering, was funded by the Department for Transport. Queen’s University head of the intelligent and sustainable infrastructure group Su Taylor says her team has been monitoring the bridge’s condition using fiber optic cables embedded in it. These were inserted among the fiber threads before they were immersed in resin – something that is impossible to do with steel as the heat of its production is too high. The findings have been better than expected. “The strain levels in the BFRP have remained consistently low,” Taylor says. She adds that the measured strains under live traffic are also far lower than those predicted by more onerous static load tests. Temporary works trials
Skanska is also putting basalt rebar to the test, although only in temporary works so far. It has worked with National Highways on a trial of its use in a temporary works access road and as part of Skanska Costain Stribog JV in temporary guide walls for diaphragm wall work on HS2. For the National Highways trial Skanska constructed a temporary works access road to junction 6 of the M42 using various concrete slab combinations. The trial tested BFRP in combination with traditional concrete and low carbon concrete, compared with steel in the same conditions. “Combining low carbon concrete with the basalt fibre reinforcement was an innovation that hadn’t been done before,” explains Skanska chief engineer and trial leader Paul Cole. Over the course of the trial, the various slabs on the temporary access road were monitored for flexural strength, shear strength and pull-out. In all cases the BFRP slabs outperformed expectations and yielded “impressive and comparable results” next to the steel-reinforced slabs, according to Cole.In terms of shear strength, the BFRP slabs held up better under an applied load than the steel reinforced slabs. The BFRP reinforced concrete reached a maximum strength of 141.5kN with classic concrete and 106.1kN with low carbon concrete, while steel-reinforced concrete reached 110.1kN and 97.5kN, respectively. This was a surprise to Cole who said it was the area he was most concerned about. He explains: “Steel is a homogenous product, but basalt fiber isn’t – all the strands are lined up in one direction. It’s twice as strong if you try to pull it out, but it performs less well than steel if you try to cut through it.” While the shear results are “brilliant”, Cole would like to do more trialing in that area. Its use on the HS2 guide walls revealed other benefits. Skanska project director Deon Loud explains: “You don’t need a hot works permit to cut it, because it’s like cutting rock – there are no sparks that come with it.” Loud and Cole say there are musculoskeletal benefits for site workers, as well as speed and efficiency gains, as basalt reinforcement is much lighter than comparable materials. Loud says the guide walls were finished in half the time because the bars could be lifted by hand. There are huge potential benefits from using BFRP and the Thompson’s Bridge scheme has proved those in the long term. Nonetheless, more testing is needed to allow the material to become as mainstream as steel in the UK.
Recent Comments