With hype around the metaverse becoming a reality, what does it mean for civil engineering firms, the construction industry and infrastructure projects? As metaverse digital environments start to take shape, all sorts of industries are striving to get ahead of the curve. Bloomberg predicts global metaverse revenue of $800M (£650M) by 2024 and the construction industry has been quicker out of the blocks than usual when it comes to adopting emerging technology. In essence, the metaverse is a digital environment that functions as a reflection of the real world. In the metaverse human beings can interact socially and economically through avatars. In short, it is a new world in which to live. While the social metaverse may still seem some way off from being mainstream, Autodesk technology strategist Alexander Stern believes the industrial metaverse is already here. Stern describes the industrial metaverse as providing “a connection between digital models and the built world, the construction site and all the stakeholders involved in a construction project”. The social metaverse allows everyday activities such as working, meeting friends and attending concerts or sporting events to be carried out in a virtual realm. Stern says its existence can make the metaverse seem “trivial, frivolous and irrelevant for business”. He adds: “The industrial metaverse is very different. VR (virtual reality), AR (augmented reality) and mixed reality applications are already available and can already bring significant efficiency to construction projects.” At Autodesk, metaverse technology has already been used on numerous projects. As an example, Stern points to the use of VR and gamification to “troubleshoot real design problems before construction” on the Bergensbanen (Bergen Line), the railway between Oslo and Bergen in Norway. VR and AR technologies were also used by Autodesk to create an immersive exhibit for the proposed reconstruction of Notre Dame cathedral in Paris following the devastating fire in April 2019. Using these technologies has allowed the public to explore and interact with the planned rebuild in an immersive 3D environment. “In the construction space, we believe that the metaverse is a technology that will significantly improve collaboration when designing, simulating and building something,” Stern points out. He says that the way this technology improves collaboration is by making communication between stakeholders easier. Communication in collaboration is essential [but] ambiguous environments such as construction invite significant room for misunderstanding. Immersive metaverse technology can help clarify and smooth communication without the need for frequent site visits.”
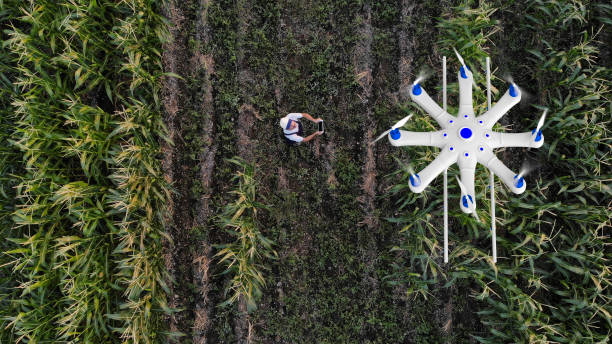
Bentley Systems Digital innovation Laboratory.
senior director Greg Demchak agrees that improved collaboration is an important benefit for those having “immersive experiences” through metaverse-powered technologies like VR and AR. Demchak adds that the technology could boost stakeholder engagement and allow teams to identify risks faster. He says: “In fact, with a 1:1 scale virtual reality experience, it is more likely the issues will be spotted before they become a problem in the field. “In addition to reducing risk and rework, the metaverse enables a multi-user experience of 3D/4D models that is spatial in nature. This goes beyond reviewing documents or sharing a screen of a 3D model in a Teams/Zoom call and allows people to interact directly in the virtual model.” The construction industry can also benefit from the greater situational awareness offered by the metaverse, says Demchak. It can have a positive impact on trade coordination, construction rehearsals and site safety training, he adds. Demchak believes that several facets of the construction sector, from design to assisting with public buy-in during the consultation phase, could gain from metaverse technology. The industry is acknowledging these benefits and for this reason many traditional contractors are investing in the technology. Spanish engineering giant Ferrovial, unveiled its Infraverse platform earlier this year. It harnesses metaverse technology to solve real-world infrastructure problems. The Spanish contractor describes its Infraverse as “a virtual platform from which to transform, develop and improve its assets and operations”. In reality, the Infraverse brings together technologies such as VR, AR, artificial intelligence, simulation technologies, building information modelling (BIM) and digital twins. For its creation, Ferrovial has partnered with major technology companies including Autodesk, Bentley Systems, Nvidia and Microsoft plus gaming giants Unity and Unreal Engine. Ferrovial head of asset management and process digitisation Darren Anderson explains that the “Infraverse can be many different things for many different purposes […] it is something very different for every project.”
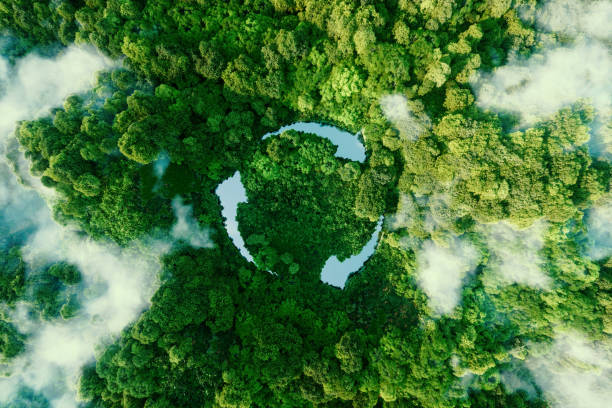
He adds: “The Infraverse is made up of different things.
Think of it as a suite of immersive digital solutions that can be selected when appropriate based on a project’s focus and its aims.” Ferrovial has used its suite of Infraverse technologies on 10 major projects so far and has generated 100 business cases. The projects include using artificial intelligence-driven crowd simulators to help design highways and airport terminals. It can also be used to provide health and safety training in the virtual world for those working on dangerous sites, for example when work at height is required. Ferrovial has also built a series of Infraverse labs with floor to ceiling screens on each of the four walls. The laboratories can connect with one another to enable collaboration around the world. Currently Ferrovial has laboratories in London, Madrid and Austin in Texas and has plans to install more later this year. Anderson says that the main focus of the Infraverse is to provide a digital focus for an asset’s full lifecycle. He adds: “From immersing design teams in a digital twin during the early development phases to helping with public consultations, to training onsite teams, to changing the BIM model during construction and then through to monitoring and maintaining the asset after construction, metaverse technology can be used and it should be viewed as a tool to be used throughout an asset’s full lifecycle.”
Recent Comments