Engineers working on the Silvertown Tunnel have successfully rotated the first 1,400t section of the UK’s largest tunnel boring machine (TBM) 180° in the reception chamber using an innovative “nitrogen skate” system. The Silvertown Tunnel is a new twin-bore road tunnel currently under construction beneath the River Thames between Silvertown and Greenwich. It is being delivered by Riverlinx CJV, a joint venture of Bam Nuttall, Ferrovial and SK Ecoplant, for Transport for London. On 15 February the TBM broke through at Greenwich, on the south side of the river, having completed the 1.1km drive for the southbound tunnel. Most twin-bore tunnels either use two TBMs or dismantle the single TBM and return it to the initial launch point for its second drive. The site, time and financial constraints on the Silvertown Tunnel project meant that the team decided to devise a way to rotate the machine 180° and send it back under the river to bore the northbound 1.1km tunnel. “This was the most efficient way of doing the two tunnels from a cost perspective and a programme perspective,” Riverlinx operations director Borja Trashorras said. “And in doing so, we’ve done it in the most innovative way that we could, in a way which has never been done before in the UK.” TBMs have been rotated in a similar manner in Paris and Stuttgart, Trashorras explained, but in both cases it was just to make the extraction of the machines easier – not to bore another tunnel. It has also never been done with a machine this large. The Silvertown Tunnel TBM is 82m long from cutter head to the end of its backup gantries and the cutter head has a 12m diameter. The tunnelling shield alone is 19m long from cutter head to the rear of the screw conveyor and weighs 1,400t.
How engineers at Silvertown Tunnel Are Using ‘Nitrogen skates’ for a record-Breaking TBM Rotation
by News | Mar 24, 2023 | India | 0 comments
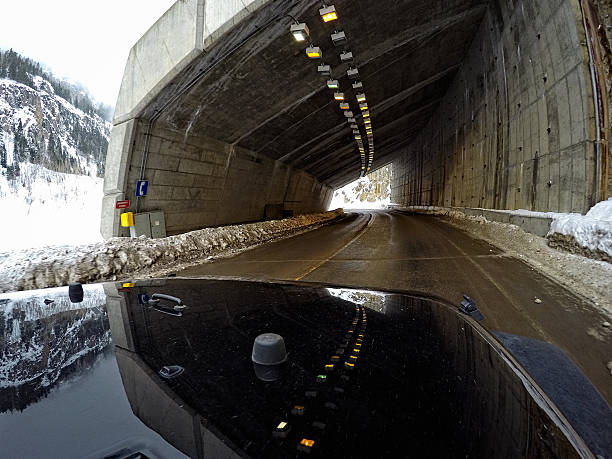
Recent Comments