A new government framework could boost the uptake of modern methods of construction (MMC), but questions about the accuracy of measuring the proportion of offsite construction in projects remain. We need to fundamentally change our views about design and procurement to enable the uptake of Modern Methods of Construction (MMC), argues Mace global leader of cost and commercial management Andrew Beard. MMC encompasses a range of approaches including offsite manufacturing and new onsite techniques. It offers advantages over traditional construction in terms of programmed, waste, carbon and safety. Beard, like many supporters of MMC, says that the far reaching step change to widen its use should include new ways of thinking about construction delivery. These include design for manufacture and assembly (DfMA), which fosters a predesigned “whole of project” approach to designing the component parts of a scheme and even the process by which they will be produced and assembled on site. But a barrier to progress in this area is the need to rethink the concept and calculation of premanufactured value (PMV) used in project procurement. PMV is a core metric for measuring the level of MMC in a project and is central to the UK government’s procurement programmer. To secure a contract, contractors are required to show that pre-manufacturing will account for 70% of their construction cost. It has become a critical topic because the government’s drive to boost MMC uptake is again on the agenda. On 24 January, government procurement agency Crown Commercial Service (CCS) ushered in a new offsite construction framework called Offsite Construction Solutions. The framework replaces CCS’s Modular Solutions Framework which closed on 1 April. It covers a broader range of manufactured and prefabricated building systems and components, specifically 2D panelized structural systems and panelized external building retrofits. It has been designed for use by public sector clients to promote the standardization of building design across government property, with a focus on the health, housing, education, justice and defense sectors. As constructors move to respond, the accurate calculation PMV – particularly for the purposes of tendering – is gaining prominence. Definition issue Sir Robert McAlpine head of MMC Scott Tacti says PMV presents challenges in its current form.
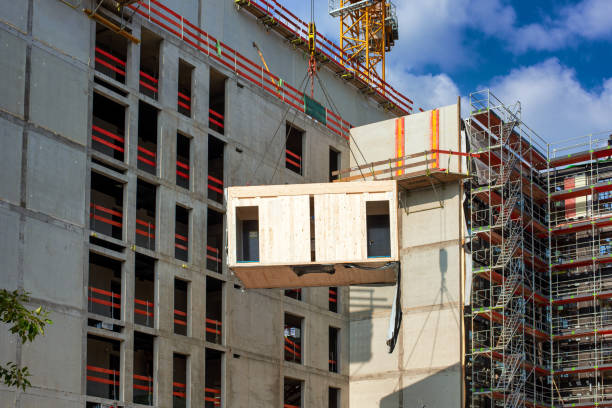
In Fact, “Current Form” is a Stretch, Mainly Because.
PMV has yet to be comprehensively defined and applied. Tacti says Sir Robert McAlpine uses its own PMV calculation to subtract inputs including labor on site and prelims such as site accommodation or craneage from gross cost. The Construction Leadership Council (CLC) has its own similar definition of PMV, widely recognized by the industry. It is described as the financial proportion of a construction project’s gross construction cost derived through pre-manufacturing. This relates to the 70% figure required by many public sector schemes. Tacti questions the accuracy of PMV as it is currently being used. “Up until the point that contractors have tender returns and the supply chain can confirm a project’s actual on-site costs, PMV is an estimate,” he says. “In the early stages of a contract, the number relies on estimators understanding the breakdown of materials, labor and plant, both off site and on site. We need greater education about PMV within the wider industry and standardization of how PMV is calculated. ”Beard agrees: “I do not think we have an industry wide definition of PMV that stands up. Whether it is supported by the CLC, whether it’s endorsed by the Royal Institution of Chartered Surveyors (RICS), whether it’s administered by the ICE, we need that pan-professional body that says, ‘this is the standard and this is how we’re all going to use it’.” He believes PMV should be used like other standard metrics such as cost per square meter. “When we talk about that, we have clear guidance from the RICS about what constitutes a close gross internal floor area or a net internal floor area. We need the same level of definition, understanding and adoption across the industry to provide a credible dimension to PMV.” Modular & Portable Building Association development director Richard Hopkins goes further, stressing that PMV should encompass much more than a cost-based calculation. “When you read the [CLC] definition, it appears to have been written by a quantity surveyor. It is a commercial metric,” he says. “I think PMV needs to be more of an engineered calculation than a commercial calculation.” It also fails to account for the complexity and range of jobs, he says. MMC has its origins in small scale residential housing, but is now used on major projects, from hospitals to infrastructure. The scale, diversity and complexity of projects on which it is used also adds to the confusion about PMV’s accuracy, Hopkins says.
“In The Civil Engineering Context, if I Take Off-Site Bridge.
construction as an example, the M40 was recently closed for three or four days so a major off-site bridge construction could go in. “A high proportion of the cost of that project might be related to the road closure. “That has nothing to do with the construction element being on site or off site. Where does that element of the contract go in the current PMV calculation? The more costs that you’ve got that are not related to offsite, be they incidental like a road closure or the environment of the construction site, the worse it’s going to make your commercial PMV value, which doesn’t necessarily reflect the overall value of the project. ”Early engagement Beard believes that while standardizing and accurately calculating PMV are critical, fundamental changes to the construction delivery model are also needed “That starts with how projects or programmers are being set up and incentivized,” he says. He adds that the responsibility of each contributor in the construction value chain for the PMV must be more clearly defined. “For example, I would suggest that a designer who is creating that design is also thinking about the build strategy for design, in other words, how it is constructed,” he says. “This is the point about DfMA and procurement for it because they happen earlier in the cycle than a traditional project. If you think about the designer who is creating that design and is also thinking about how it is built, they should also be thinking about what sub-assemblies and systems and products they might be using and how that design is put together. ”Tacti stresses that earlier engagement for every project stakeholder is important. Too often the industry is considering PMV at the late stages of a project and without supply chain consultation or integration. It is my opinion that architects and engineers should develop schemes with an eye on PMV from Royal Institute of British Architects (Riba) Stage 1 [preparation and brief stage]. “However, the truth is almost entirely the opposite. Most of the schemes have zero reference to buildability, let alone the advantages in productivity, performance, quality, lifecycle cost or carbon that MMC could bring. “About 60% to 70% of these opportunities are lost by [the time a project reaches] Riba Stage 3 [development and design stage]. Unfortunately, this means projects are unwittingly wasting budget as they rely on outdated architectural and engineering practices.” Calculator
The idea of making PMV calculation widely accessible through digitally enabled calculators is also a topic for discussion among MMC players. “It would be good to see a standard calculation tool that can be regulated, legislated,” says Hipkiss. “It is important to push the point that we should be seeing a target and an achieved PMV. So, it gives the industry a benchmark to work towards.”
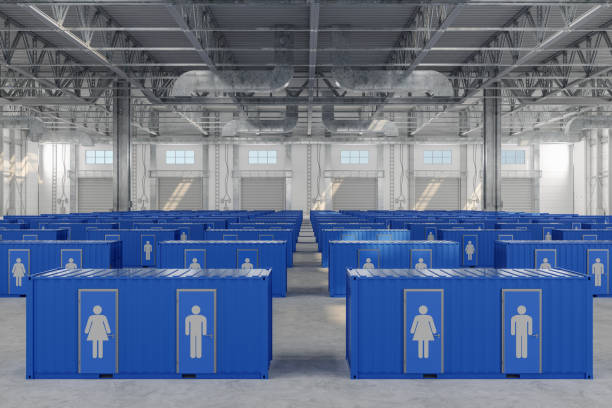
He Says Widely Used Carbon Calculators Could Potentially.
form the basis for PMV calculators. “One of the big benefits of pre-manufacturing or offsite construction or modular construction is lower embodied carbon. So, you could almost use one of the standard carbon calculators as a basis but add other PMV metrics to it,” Hopkins explains. Techy agrees: “In the area of carbon management, we now have [lifecycle assessment calculator] OneClickLCA, which has become the benchmark tool for many project teams. It would not be an insurmountable task for a similar tool to be enhanced to include PMV calculations.” Data availability Looking ahead, Tacchi says published data will be a critical part of solving the PMV riddle. “Currently no data from public sector use of PMV is being published, while the private sector has almost zero adoption of PMV – and perhaps a limited understanding,” he says. “At Sir Robert McAlpine, we undertake a detailed MMC and PMV assessment on every tender to identify opportunities to improve productivity through MMC and contemporary innovation for our project delivery and our clients. “Over the next few years, this will allow us to benchmark project against project and develop MMC best practice, underpinned by reliable data.” In a previous role, Tacchi ran the Department for Education Off-Site Construction Programmer. He says a key lesson that stayed with him is the ethos of data-driven decision making. “If we do not have accurate data, then we do not make accurate decisions,” he explains. “If, as an industry, we do not get to grips with a rationalized approach to comparing one project’s productivity against another, benchmarking best practice, then we will continue on the merry go round of low productivity statistics for another 30 years.”
Recent Comments