An exploratory tunnel driven ahead of the main Brenner Base Tunnel bores through the Alps is helping contractors meet the challenges in building the world’s longest underground railway corridor. Tunnelling through robust rock with complex fault zones – fractures between two blocks of rock – is characterising construction of the Brenner Base Tunnel. The fault zones are compelling project engineers and operatives alike to think laterally and hard as they work on the new rail link between Austria and Italy. To gain early insight into the ground conditions, an exploratory tunnel is being bored in advance of the main tunnels to help ensure safe, timely and economic construction. The Brenner Base Tunnel for the new rail line is being driven beneath the Brenner Pass on the Italian/Austrian border at a total project cost of £13.2bn. The project client is BBT SE, which is formed by Austrian railway company Österreichische Bundesbahnen and Tunnel Ferroviaro del Brennero of Italy. The Italian partner is composed of Ferrovie dello State Italian and the Provinces of Bolzano Trento and Veronawith. Funding is provided by the European Union as well as the Italian and Austrian governments. The completed tunnel will enable rapid transit by rail between Innsbruck in Austria and the Italian town of Fortezza, with travel time expected to be reduced from 80 to 25 minutes. The tunnel will consist of two main single track 8.1m diameter bores between 40m and 70m apart. The new bores are 55km long and will connect to the existing Inn Valley tunnel just south of Innsbruck to create a 64km long railway tunnel – the longest in the world. It has been designed to provide a technical service life of 200 years. Work began on site in 2007 and is divided into seven packages, known locally as lots (see diagram). The lots are designated: H21 Sill Gorge; H41 Sill Gorge-Pfons; H33 Tulfes-Pfons; H52 Hochstegen; H53 Pfons-Brenner; H61 Mules and H71 Isarco River underpass. Tunnelling is challenging, as there are four main rock types – Innsbruck quartzphyllite, schist, gneiss and granite – blighted by faults.
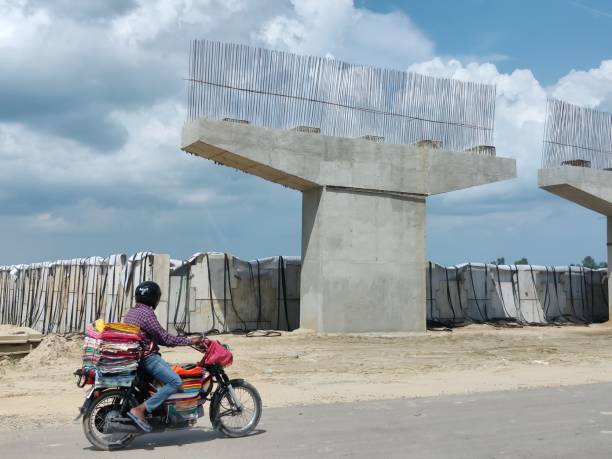
Exploratory Tunnel
The Brenner Base Tunnel is deep, running as much as 1.72km below ground level. This made it difficult, to investigate conclusively from the surface the geological make-up of the ground for the tunnel alignment before construction began. This, despite 35km of boreholes having been sunk from the surface. Then came the proposal to bore a 5m diameter exploratory tunnel to gain more precise geotechnical information. BBT SE Italian head of engineering and planning David Marini says: “Such a procedure is not usual in Italy or Austria. “What gave the idea more traction was that later, the [exploratory] tunnel could be used for logistical purposes including muck away on conveyors and delivery of precast elements by train.” This would provide distinct practical and environmental benefits, with enhanced access and reduced above ground transport impacts. “Later still,” adds Marini, “the exploratory tunnel will be used for drainage purposes and maintenance.”In practice, the exploratory tunnel procedure has functioned well and proven a boon to construction activity. “The exploratory tunnel runs between, but about 12m below, the main tunnels. Its excavation always precedes the main drives by at least 500m,” Marini says. “Through exploring the rock mass and rock behaviour, we’ve been able to optimise, where necessary, the executive design of the main tunnels with the geological, geotechnical and hydrogeological data we’ve obtained,” he adds. “This is resulting in reduced geological risks.”
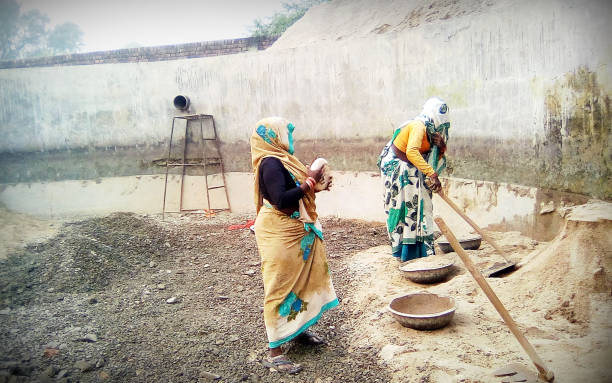
Varying Tunnelling Methods
The two main bores and the exploratory drive are being excavated using three double shield tunnel boring machines (TBMs) supplied by Herrenknecht. Contractors building the other tunnels for the project are mostly using drill and blast in stable rock conditions and mechanical excavators in fault zones. The exploratory tunnel is being excavated by a mix of methods, including use of a gripper TBM on the Austrian side. For the non-TBM excavated tunnels the ground support comes with two approaches. One is the New Austrian Tunnelling Method, where ground support, including the use of sprayed concrete linings, is added as excavation progresses. It is adapted according to ground conditions. The other method is the analysis of controlled deformation in rock and soils – or Adeco method – sometimes called the New Italian Tunnelling Method. For this, coring ahead of the tunnel face determines the excavation mode and support needed. Marini emphasises that it is essential during boring of the exploratory tunnel to have an experienced technical team in place. “This is so that data can be analysed in a timely manner, back analysis activities performed and the need for special interventions assessed in advance,” he says. Escape route cross adits are also being constructed 333m apart. A total of 230km of tunnels will be excavated for the project. Before work began, BBT SE had good knowledge of the fault zones that its contractors would encounter, in particular the Periadriatic fault zone near Mules in the north Italian province of South Tyrol. The Periadriatic Fault is known to be the most significant fault along the Alps, dividing the Eurasian and Adriatic tectonic plates. The zone’s exploratory tunnel excavation was let early on as a contract, which made it possible – at the tender stage – to consider possible impacts on the main tunnels.
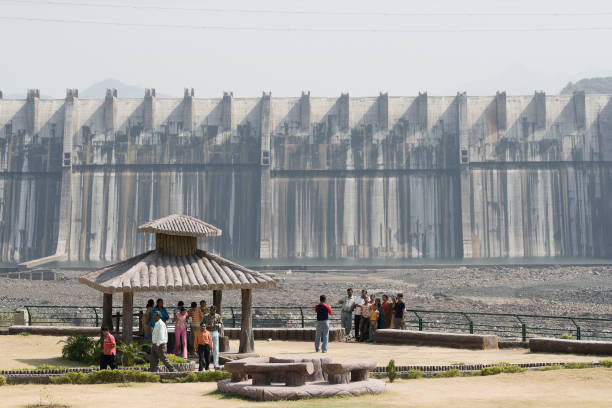
“That’s the benefit of accurate information about ground conditions,” says Marini.
Such information has greatly helped the project team decide what excavation method to adopt: mechanised – by TBM, or conventional – by drill and blast or with mechanical excavators. “TBMs can only be used in certain rock masses, where the rock mass is not squeezing,” Marini says. Where squeezing occurs, a TBM – especially a shielded one – can easily get stuck in the rock mass, causing real problems. Heavy deformation of segmental lining at a fault met in the Periadriatic zone brought one TBM to a standstill for four months. “The advantage of TBMs with advanced technology is that they increase safety for workers and, for excavations of a certain length [more than 3km] and shorten construction times. That said, conventional tunnelling is much more flexible during the execution of tunnelling works, and therefore more efficient especially in crossing fault zones,” Marini says.
Challenges
Fault zones are by no means the only problems being faced. New challenges are continually coming up, according to Marini. They include contractual as well as technical ones. “On one construction lot, for example, the existing contract had to be dissolved which meant new tender procedures had to be launched,” he says.
The workforce also has to contend with pressure.
“Working underground is a constant challenge for workers: they work, in shifts, 24 hours a day, seven days a week and spend more than eight hours in the tunnel. And it can take almost an hour to reach a TBM from the tunnel entrance. “During excavation of the exploratory tunnel there is no certainty as to how the rock mass to be excavated will behave. “Sometimes special operations are required and workers must also be prepared for these.” One particular technical development has been proving beneficial to those working in parts of the Brenner Base tunnel. A so-called multi-service vehicle (MSV) is a highly innovative self driving supply truck, being used for the first time on the construction site at Ahrental. Its function is to supply the TBMs with tunnel lining segments and other materials.
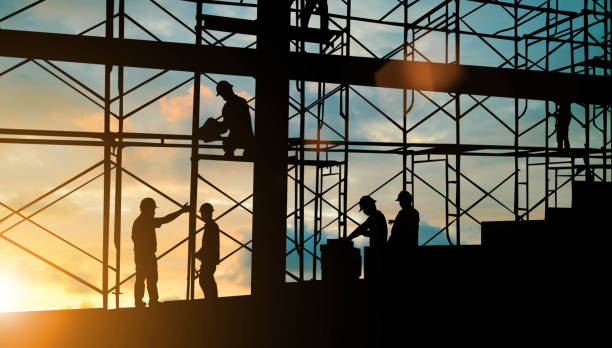
Tunnelling progress
Excavation of 152km of the tunnels is already complete. Tunnelling for the H33 Pfons – Tulfes Lot was completed last September and work on five other sites has been progressing. Nearest to completion is the H71 Isarco river underpass, which will connect the Brenner Base tunnel to the existing Brenner line and the Fortezza train station. It is 97% complete with completion due in 2023. The H61, extending from the Isarco underpass lot area to the Austrian border, is 88% complete. Tendering for the £764M Pfons-Brenner construction lot (H53) started in January 2022. For this, 25.2km of main tunnels are to be excavated, of which approximately 15.2km using a TBM and around 10km by blasting. The contract will also involve the excavation of 1.3km of exploratory tunnel. About 2,000 workers are employed on the Brenner Base Tunnel, in Austria and Italy combined. By the time the tunnel fully opens in 2032, some staff and operatives will have been employed on it for most or all of their working lives. Marini and his colleagues are emphatic that the Brenner Base tunnel project has impeccable environmental credentials. He says: “The tunnel itself is a project for the environment, designed to shift the transport of goods and people from the road to the railway. “In the construction phase we also look to respect the environment, for instance building factories for precast elements directly on the construction sites instead of far away, as well as the use of conveyor belts for the transport of excavation materials.” To convey the importance of the Brenner Base tunnel project, members of the public including school children can visit the site once a week in small groups, underground, to see excavation taking place. There is also an annual information day open to all. The last one was attended by 2,500 people. “We are keen to promote transparency, understanding and goodwill,” Marini says. “After all, we’re here for a long time.”
Recent Comments